In today’s fast-paced and competitive market, the ability to adapt swiftly is crucial for success. 3D printing has emerged as a transformative technology, providing companies with unparalleled flexibility and speed in end-part production. This innovation is not just about fabricating parts; it’s about revolutionizing the entire production process.
The Power of 3D Printing in Modern Manufacturing.
3D printing, also known as additive manufacturing, is transforming the manufacturing industry. This groundbreaking technology builds three-dimensional objects layer by layer from digital designs.
Here’s how 3D printing is revolutionizing modern manufacturing.
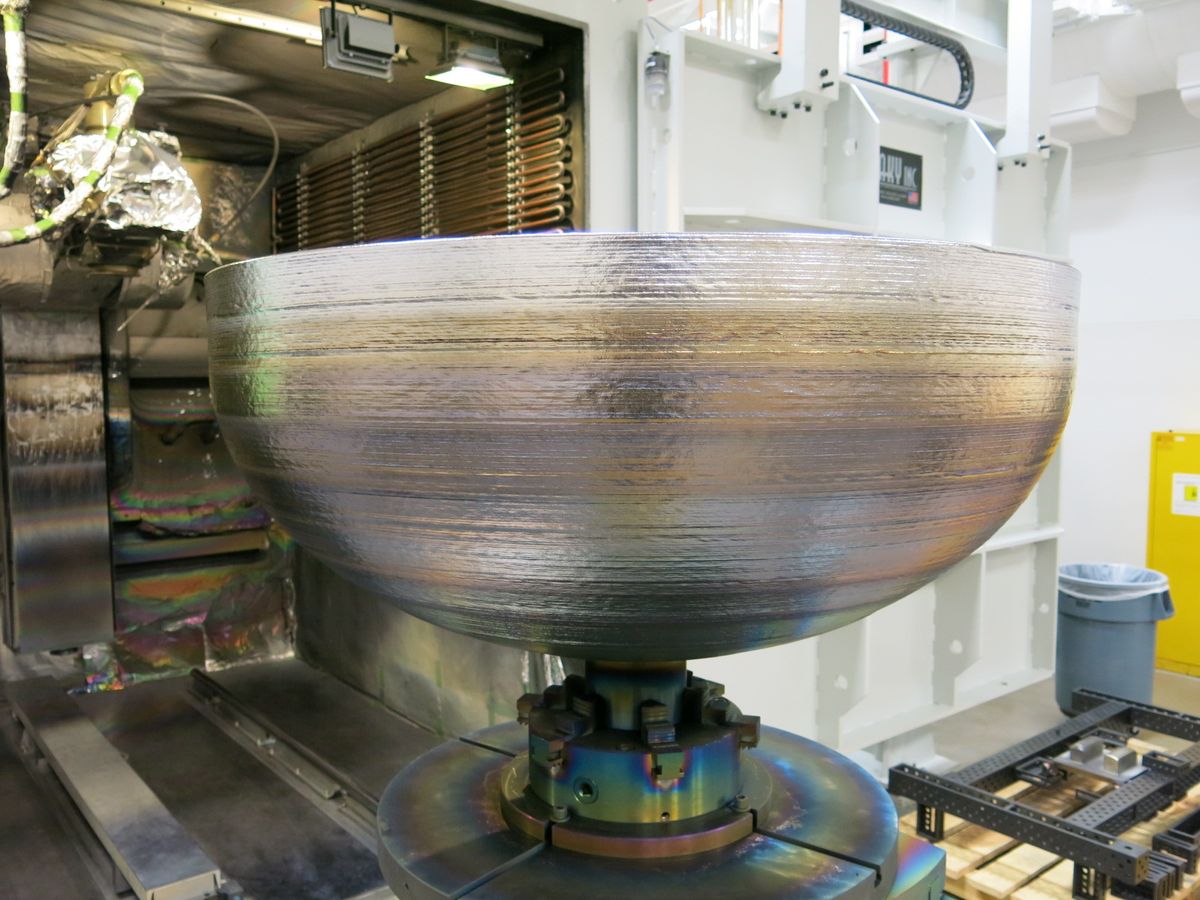
REDUCED LEAD TIME
Traditional Manufacturing: Typically, creating new products with conventional manufacturing requires custom tools for each unique design. This tooling process can take weeks or even months to complete and must be restarted entirely if there are any design changes.
Additive Manufacturing (AM): In contrast, additive manufacturing allows direct production from CAD models, eliminating the need for extensive tooling. This technology significantly reduces lead times, enabling manufacturing teams to bring products to market much faster than traditional methods.
Example: Lockheed Martin leveraged 3D printing to produce domes for large satellite fuel tanks within just three months. This was a substantial improvement compared to the two years needed with conventional manufacturing techniques.
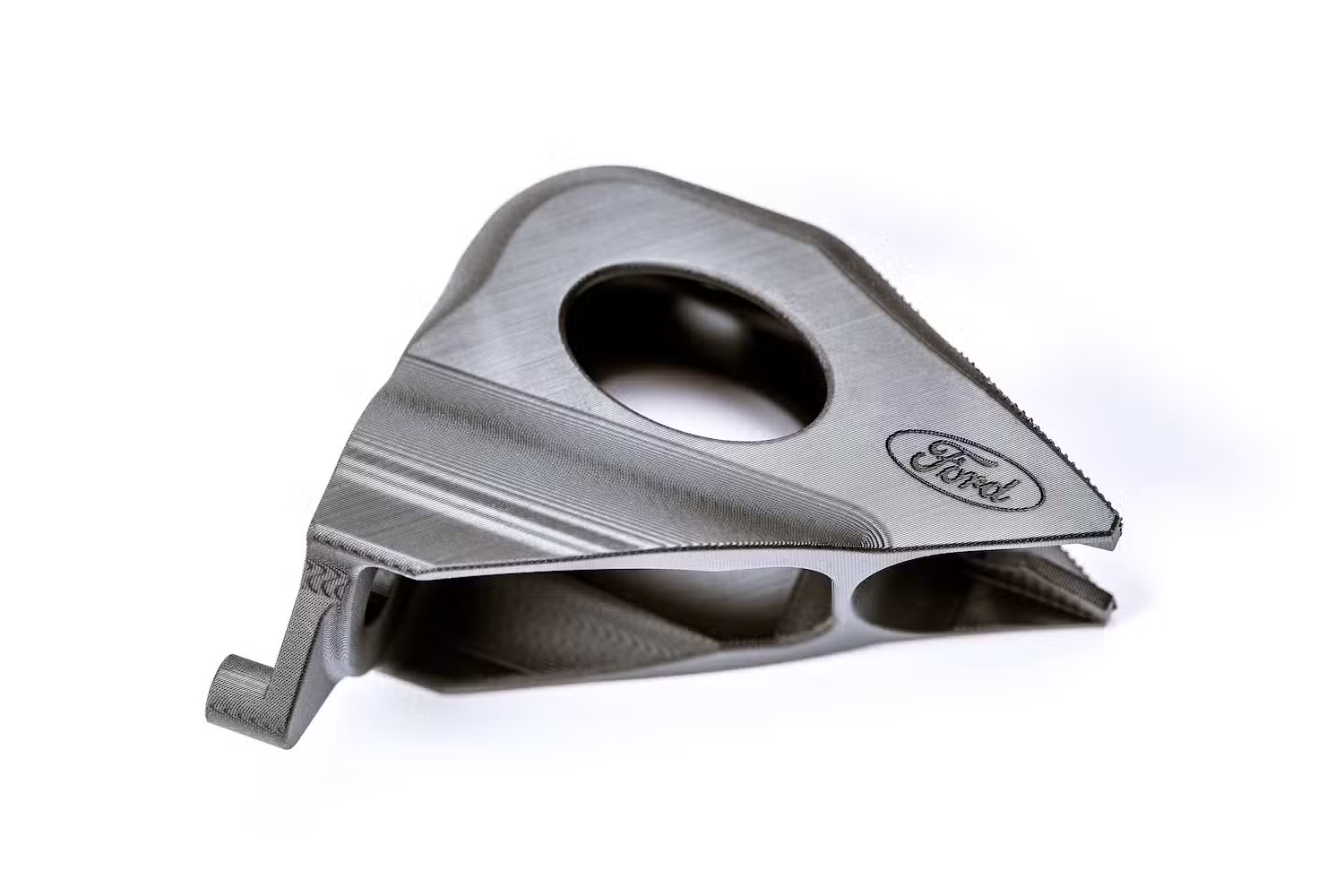
PRODUCING PARTS ON DEMAND
For businesses requiring quick production of small batches of parts, 3D printing offers significant advantages. This technology enables the on-demand creation of parts, reducing the need for large inventories and lowering storage costs. Companies are increasingly considering 3D printing for producing replacement parts as needed. It often allows for faster production of some components compared to traditional manufacturing methods, enabling swift repairs of broken parts and minimizing production downtime.
For example, Ford has implemented 3D printing technology to more efficiently meet the spare part needs of its customers and dealers.
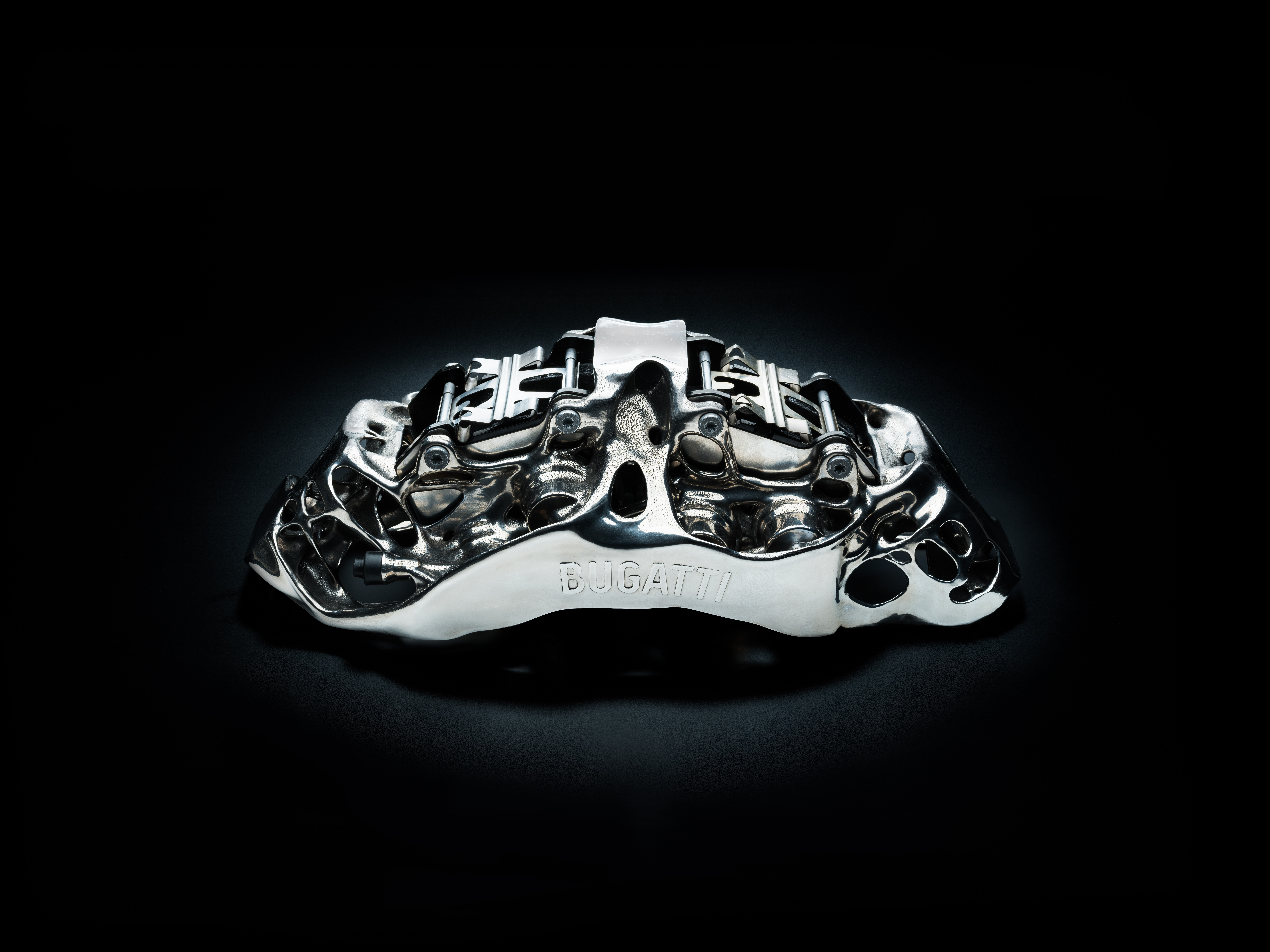
DESIGN FLEXIBILITY
In traditional manufacturing, complex designs typically raise production costs, limiting the feasibility of intricate shapes. Machining or injection molding often necessitates simpler, more cost-effective geometries. Conversely, 3D printing removes these constraints. It enables the production of intricate and complex structures without additional costs, making complex shapes as easy to produce as simple ones.
For instance, the French automaker Bugatti leveraged 3D printing to capitalize on this design flexibility in their Chiron supercar, creating what is claimed to be the world’s most powerful titanium brake caliper.
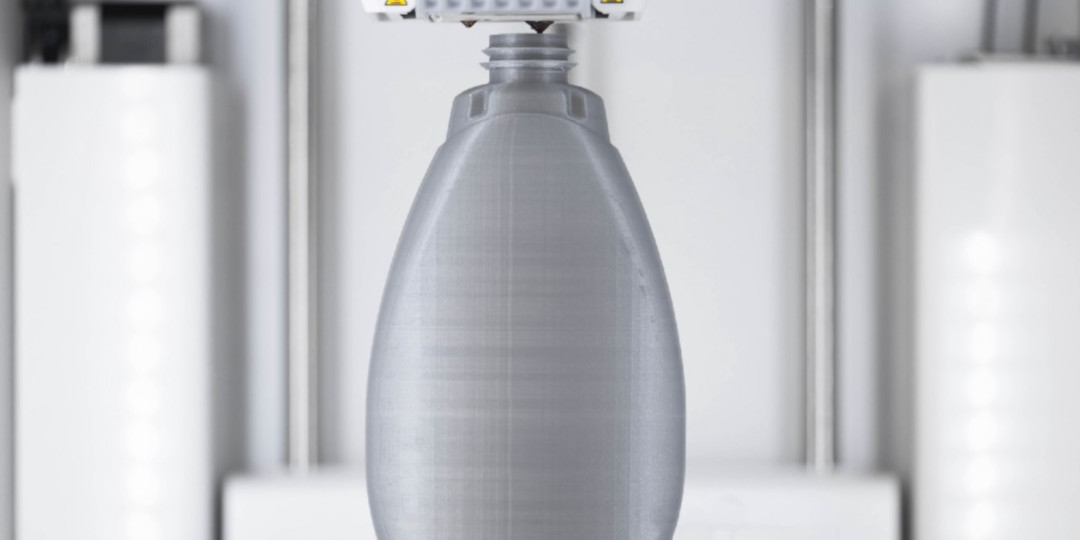
LOW VOLUME PRODUCTION
Additive Manufacturing (AM) offers a cost-effective solution for low-volume production by eliminating the need for expensive tooling such as molds. Traditional manufacturing methods require extensive tooling to be cost-efficient, typically only justifying the high costs when producing thousands of parts. In contrast, 3D printing produces parts directly from digital files, bypassing these high initial costs.
By employing 3D printing, manufacturers can efficiently produce small to medium batches of parts, substantially lowering the cost per part and reducing overhead. For instance, L’Oréal utilizes 3D printing to accelerate their product development process and shorten the time to market.
Connect with Projet:
If you’ve had a positive experience with Projet that you’d like to share, please reach out to us at [email protected]. We eagerly anticipate hearing from you.
For additional information, visit our website for comprehensive details about our services and contact information. Our friendly team is ready to assist you at any time.