3D Scanning & Reverse Engineering
Reverse engineering projects require a level of accuracy that simply cannot compromise on. Our clients trusted Projet as their go-to partner to achieve highest accuracy in their retrofitting projects.
Leverage our expertise in reverse engineering to generate 3D CAD models from existing objects (as-built), whether to determine the original design intent, modernize manufacturing processes, or design a new part to fit to a legacy product or equipment.
What is Reverse Engineering?
Reverse engineering is the process of discovering the technological principles of a device, object or system through analysis of its structure, function, and operation. It often involves taking something (e.g. a mechanical device, electronic component, or software program) apart and analysing its workings in detail to be used in maintenance or to make a new device or program that does the same thing without copying anything from the original.
The purpose is to deduce design decisions from end products with little or no additional knowledge about the procedures involved in the original production. The same techniques are currently being researched for application to legacy software systems to replace incorrect, incomplete, or otherwise unavailable documentation.
With reverse engineering, we can digitize almost anything into workable 3D CAD data. By digitizing the products and parts can modernize the manufacturing and product development processes and eliminate the need for physical inventory.
Accuracy | 0.04 mm |
Precision | 0.02 mm |
Minimum scan volume | 10 × 10 × 10 mm |
Maximum scan volume | 4 × 4 × 4 m |
Our Reverse Engineering Workflow
Place scale bars, coded targets, and markers directly on or around the surface of the object.
Scanning the object from various heights and angles until it is fully captured.
Calculate the markers, and then capture the point could using the 3D scanner and triangulate it. This produces a mesh which is typically output as an STL model. The mesh is an exact digital replica of the component, including any manufacturing variation and damage in the physical part, which will need to be accounted for when creating the final CAD model.
Our expert CAD engineers will design a complete 3D CAD model of your component based on its intended purpose. They will also create detailed 2D drawings, tailored to your needs. During this process, we can easily remove any unwanted features from the sample part to ensure the final design meets your requirements. The CAD model can be provided in your required format.
Why Projet?
As computer-aided design (CAD) has gained popularity, reverse engineering emerges as a viable method to generate a 3D virtual model of an existing physical part for use in 3D CAD or other software. Harness the power of reverse engineering to deconstruct, comprehend, and enhance existing products, fostering innovation, design refinement, and a profound understanding of complex systems. The reverse-engineering process involves measuring an object and then reconstructing it as a 3D model.
Projet is revolutionizing the way manufacturers think about—and perform—reverse engineering. We have opened the doors for managing incomplete component design data, eliminate original design flaws or failures, increase the efficiency of manufacturing processes and sustain product innovation. The following are the spheres of our retrofitting expertise:
- Parametric 3D modelling in generic and native formats
- Reconstruction from 3D scanning data, probing, 2D drawings, sketches, etc.
- Design modification from actual objects
- 3D modelling of objects of all sizes
What our reverse engineering team can do?
Projet’s reverse engineering services let you transform almost any object into usable 3D CAD data. By digitizing your products and parts, you can streamline your manufacturing and product development processes while reducing or even eliminating the need for physical inventory.
Here’s what we can do for you:
- Capture CAD data from your object
- Design a new part to fit
- Refine performance surfaces
- Update your CAD models to meet specific part-tooling requirements efficiently and accurately.
- Redesign a product or part without manufacturing defects
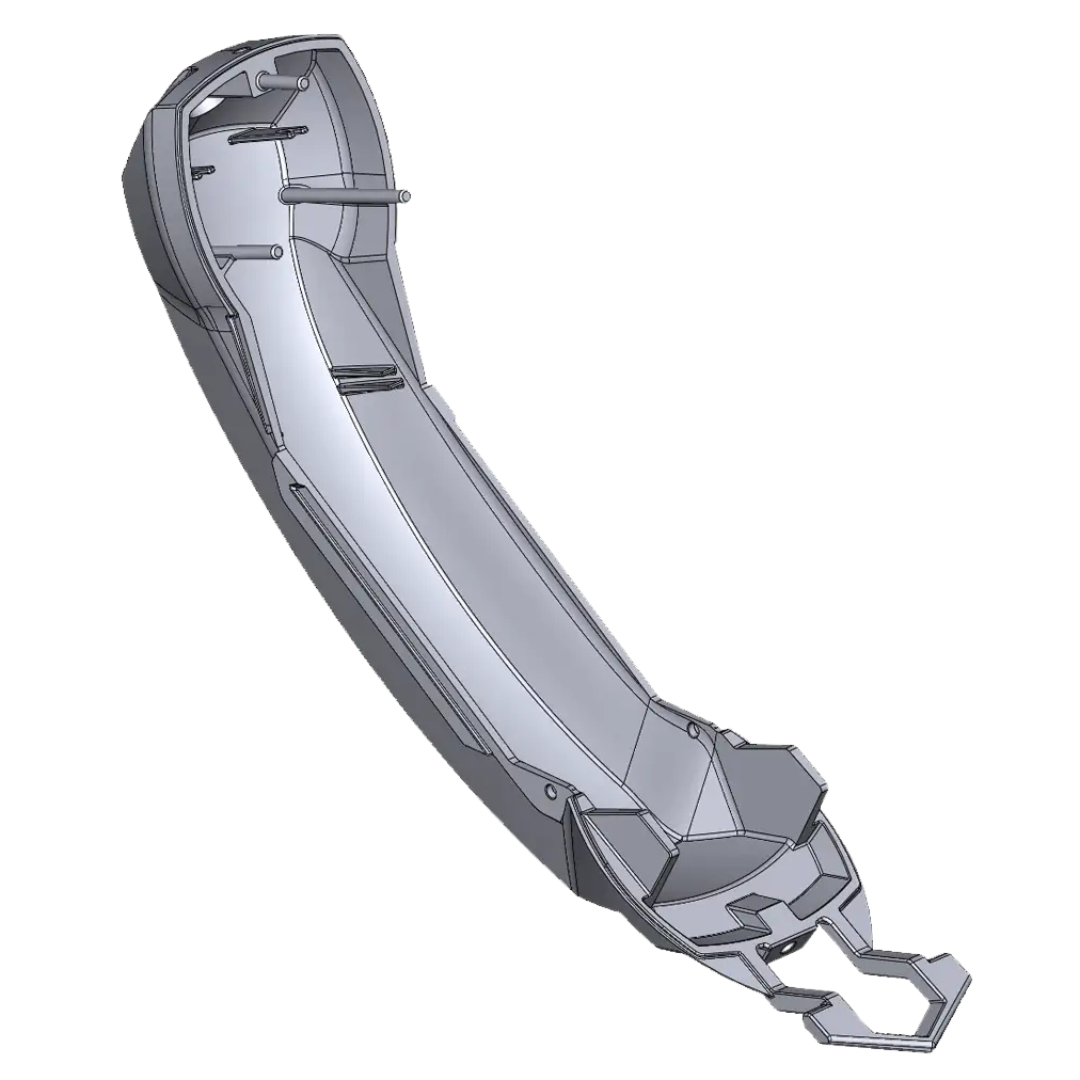
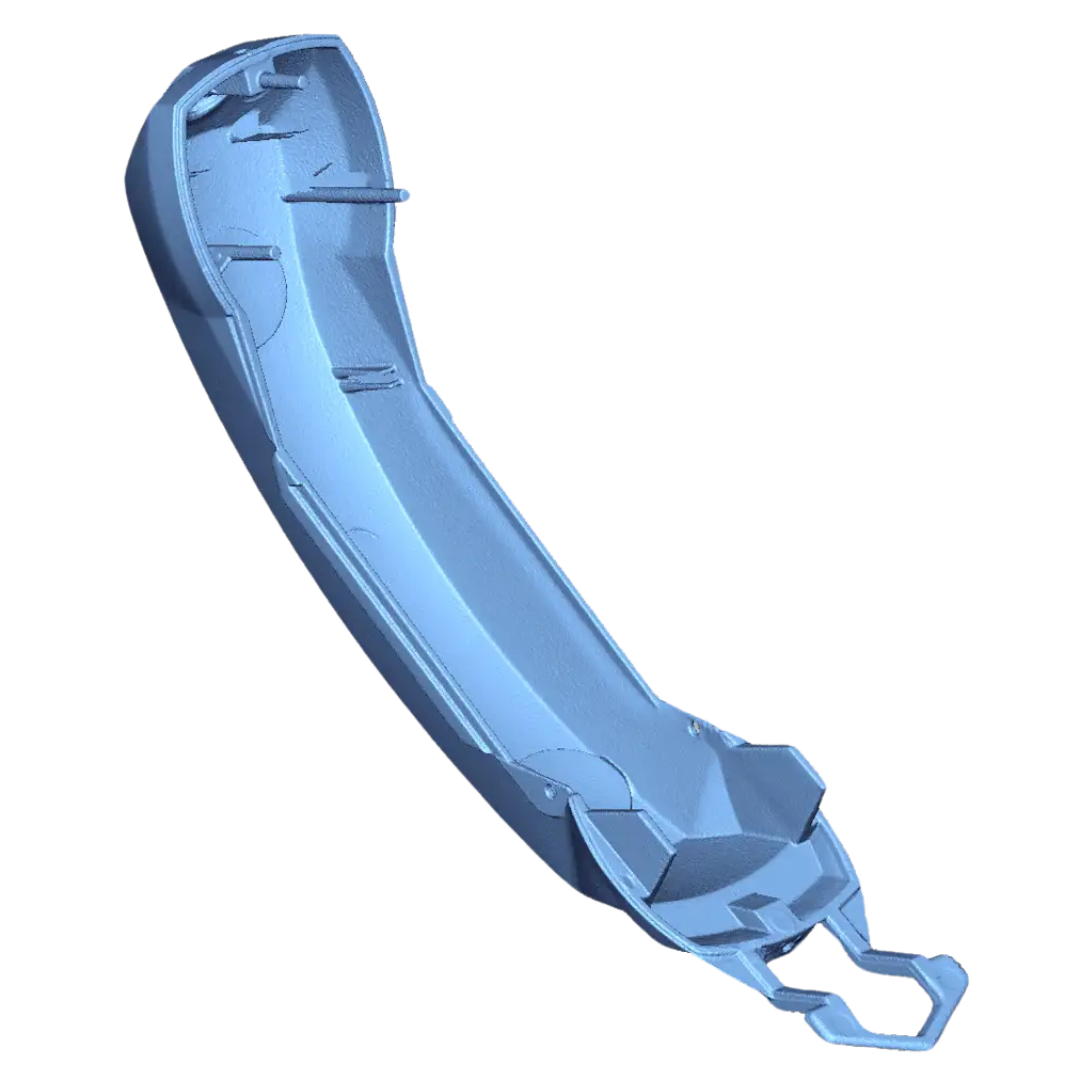
Benefits of Reverse Engineering
Reverse engineering is beneficial for many reasons, as it allows you to:
-
Complete design data:
When you have gaps in your CAD model, you can’t move forward with the manufacturing process. Reverse engineering helps you fill in those holes and make edits as needed to prepare for mass production. -
Refresh outdated designs:
If you haven’t created or updated a component in several years, you may not have a viable CAD file available. Using reverse engineering can give you a foundation for altering the part and upgrading it to adhere to modern performance standards. -
Find vulnerabilities:
Reverse engineering breaks a component down to its various functions, allowing you to find any vulnerabilities in your current design. While the CT scan alone may reveal some weak points, the CAD model will give you quantitative measures you can change. -
Create reference models:
Creating a CAD file with reverse engineering provides you with a digital model you can reference throughout the manufacturing process. Whether you rely on your new CAD model to make alterations or use it as your primary design for mass production, it will quickly prove useful. -
Document prototypes:
If you created an experimental prototype by hand, you don’t have a CAD file to reference for mass manufacturing. Reverse engineering helps you work backward from your prototype and create a blueprint for future parts.
The Purpose of Reverse Engineering
Parts Replacement | For instance, if a machine part wears out and needs replacement, particularly in the case of an older machine, certain components may no longer be in production. This can occur either because the original equipment manufacturer (OEM) has discontinued the part or has gone out of business. Reverse engineering provides a solution by allowing the digital replication of the design of the defective part. |
Failure Analysis | Reverse engineering techniques can play a valuable role in failure analysis. If a machine fails, you may need to take it apart or examine design files to determine why. Once you have this information, you know how to fix or improve the product so that it functions properly again. Examining a product using reverse engineering can reveal damaged parts of faulty designs. Looking at digital design files created through reverse engineering can also reveal flaws and help inform how you plan to repair a piece of equipment. |
Parts Improvement | Reverse engineering is also used for parts improvement. You might need to alter a component after conducting a failure analysis, or a particular might just be due for an upgrade. If no replacement or alternative part is available on the market, you could have the part reverse engineered to create a copy of the original design. From there, you could modify the design for improved performance. |
Diagnostics and Problem-Solving | Reverse engineering can also be used for diagnostics and problem-solving in a sequence of industrial processes. In a factory setting, the flow of operations can sometimes slow due to a faulty or underperforming function. When a manufacturing system consists of numerous machines and components, it can be difficult to pinpoint the source of the problem. Through reverse engineering, you can determine how everything works as one and use that knowledge to identify where things can and do go wrong. |
Our competencies
We are a highly dependable mechanical powerhouse with an extensive array of additive manufacturing (3D Printing) & subtractive manufacturing capabilities. Catering from one-off prototyping to low-volume production, we offer solutions that span from basic to industrial, including cosmetic finishing manufacturing.
3D Printing
SLS,SLA,SLM,FDM,MJF,PµSL
- Tolerances accuracy ± 0.02 mm
- Tolerances accuracy ± 0.20 mm
- Class 1 surface finishing
- Engineering grade material
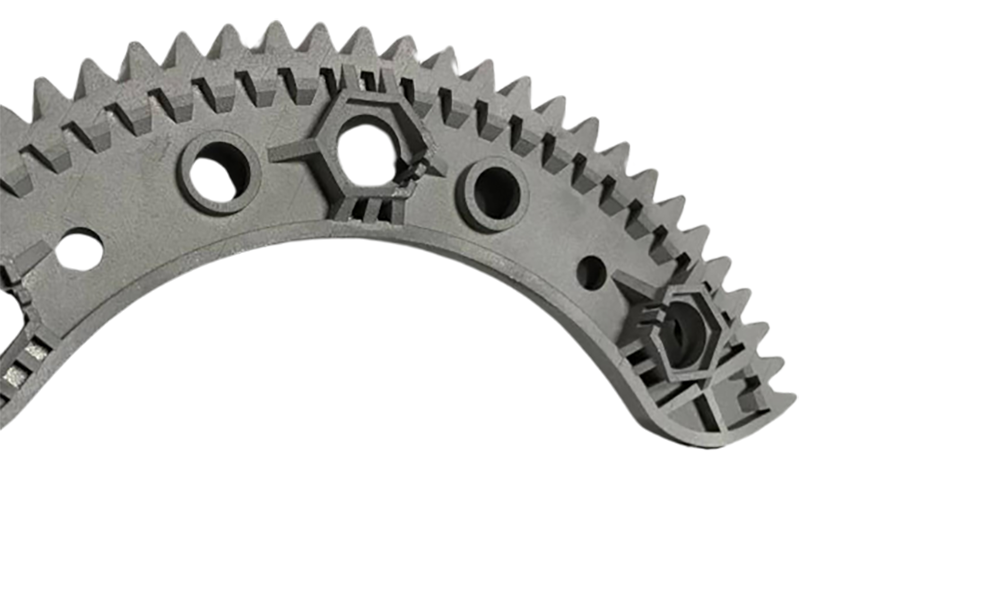
Laser Cutting
CO2 Laser
- Bending, welding
- Stainless steel, aluminium
- Thermoplastic, tapes & gaskets
- Cutting, boring, engraving, etching
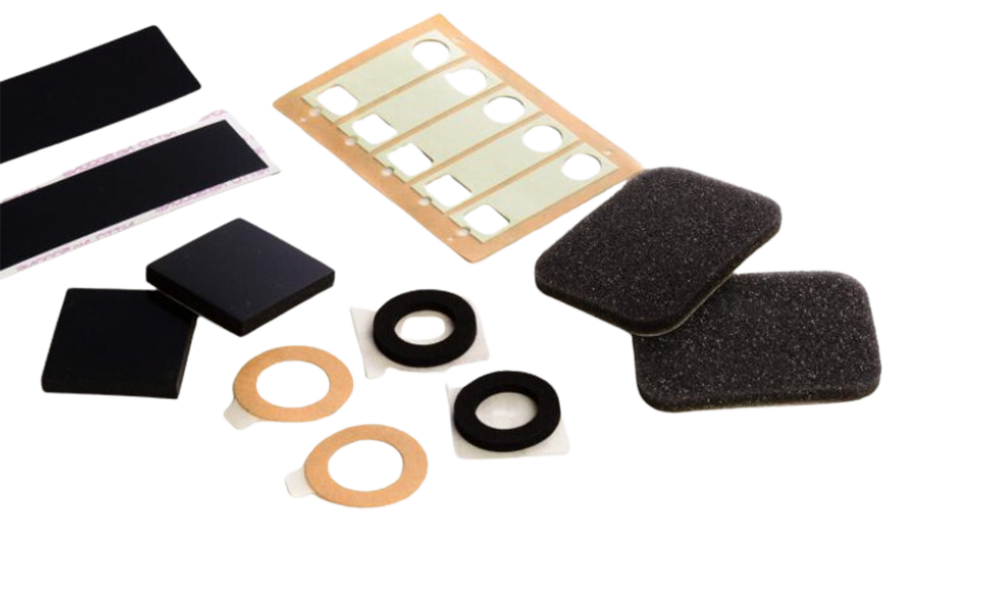
Vacuum Casting
Urethane Casting
- Material flexibility
- High transparency
- Production-like parts
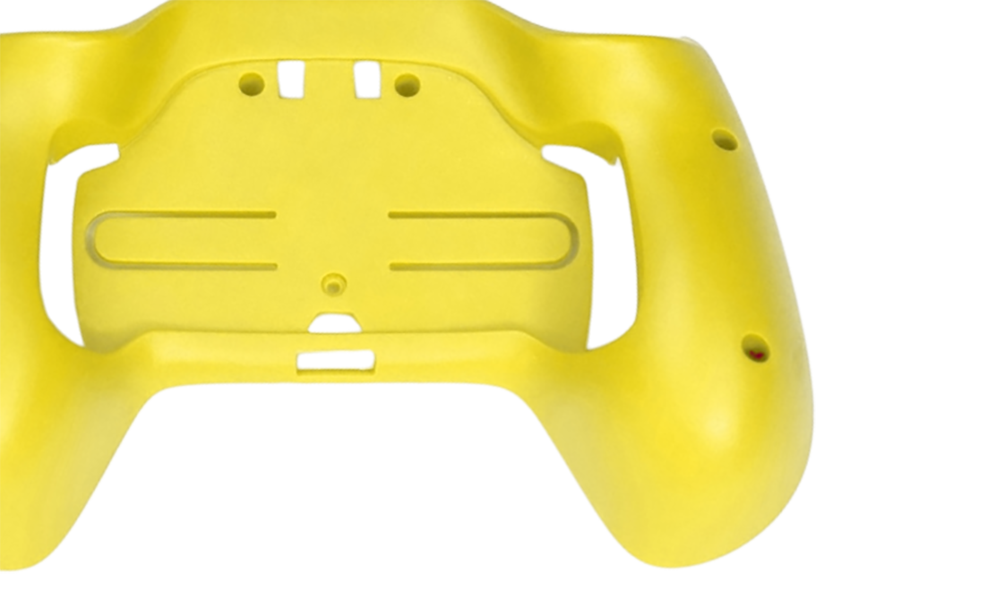
CNC Machining
Milling, Turning
- Tolerances down to ± 0.03 mm
- 3 & 5 axis
- Anodizing, powder coating
- Wide range of material
Start your next project with us today
Manufacturing limitless possibilities with industrial fabrication solutions.