Product Development & Manufacturing : From Concept to Prototype: How to Source and
3D Printing Parts for Initial Product Development
What are the best manufacturing processes for creating initial prototypes? Curious about sourcing parts for the initial prototyping stage in product development and manufacturing?
In this article, we explore effective strategies to streamline sourcing and recommend the most efficient manufacturing processes for creating prototypes with additive manufacturing.
Learn about the benefits of popular prototyping methods, including FDM (Fused Deposition Modeling) and SLA (Stereolithography), each of which can help optimize time and reduce costs. Discover how these technologies can accelerate the development cycle and ensure high-quality results, making them ideal for early-stage product validation.
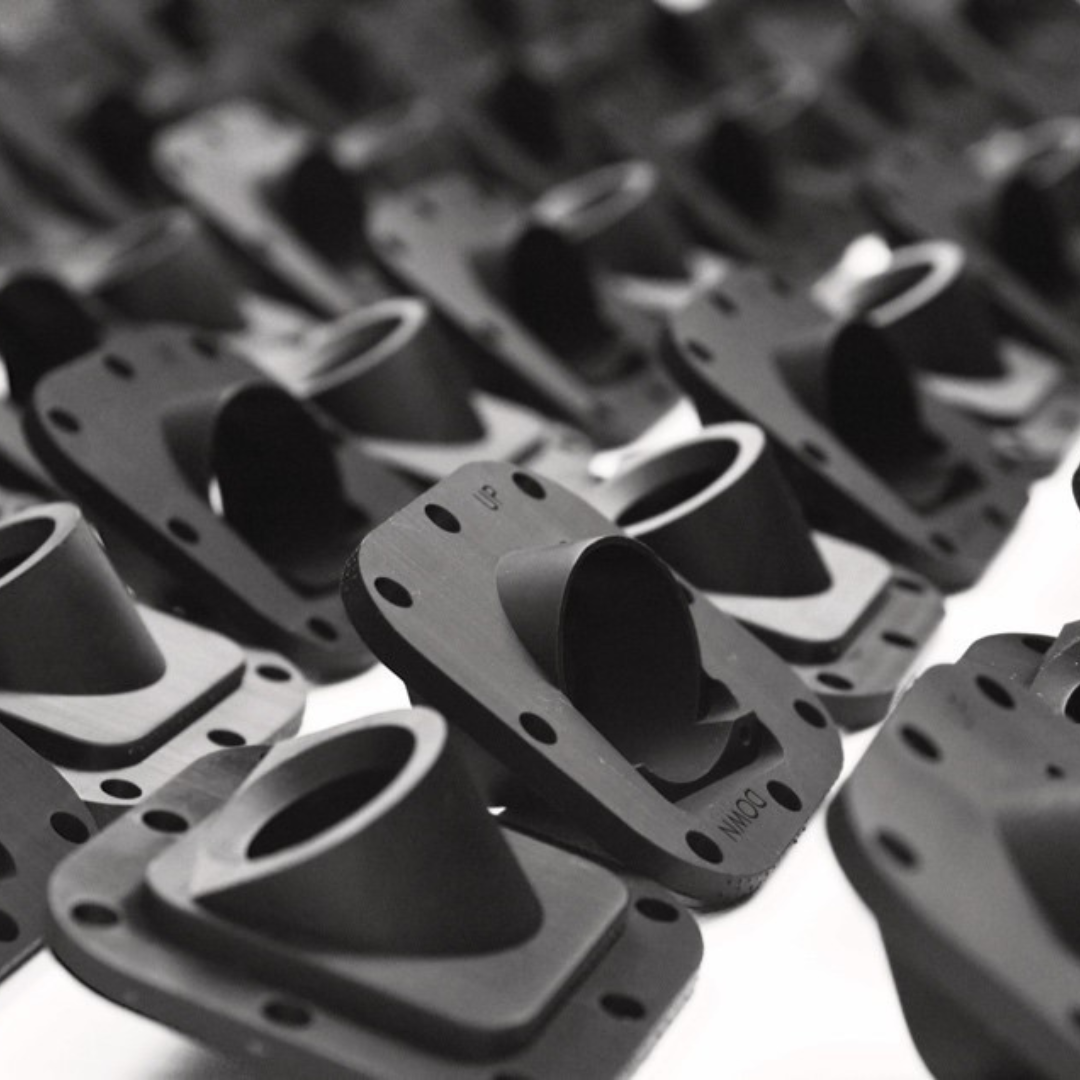
Exploring the Prototyping Phases of 3D Printing
Before launching any product, it must go through prototyping (Initial Prototype Stage). This initial phase verifies functionality, manufacturability, and assembly. Do they function as designed, and can they be manufactured reliably? Sourcing ideal suppliers, often with 3D printing capabilities, is key.
Consider the transition from CNC machining or injection molding to 3D printing early on to streamline scaling. The goal is to minimize time and costs, allowing you to move efficiently from prototype to customer-ready product without major design adjustments for each manufacturing phase.
What is an initial prototype?
An initial prototype, created early in product development, allows for testing of appearance, functionality, and user experience. An initial prototype is a foundational model created early in the product development process. It serves as a tangible representation of your product’s potential look, feel, and core functionality. This early version allows you to gather valuable insights and test key aspects of your product before investing significant resources into further development.
It can range from a basic 3D-printed model reflecting the final product’s design to a more intricate version that tests performance, helping to identify and reduce potential risks.
Prototyping ensures a stronger foundation for refined development. To ensure your design translates seamlessly from the digital realm to the physical world, initial prototyping is a critical first step. By quickly testing your design’s functionality, you can identify potential issues and iterate accordingly.
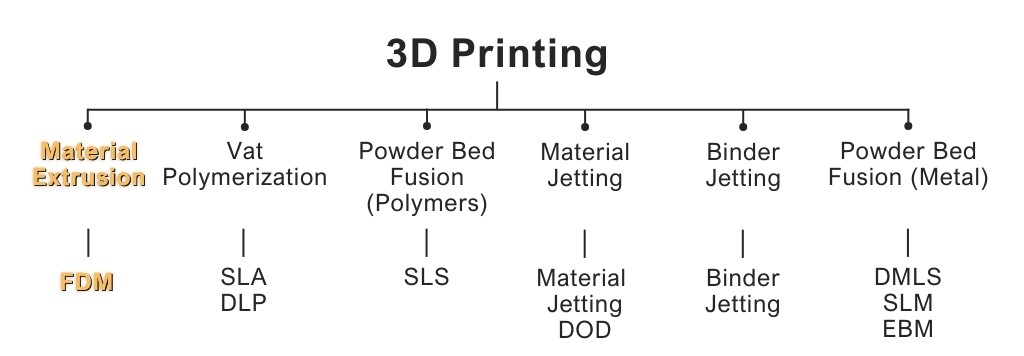
The Benefits of Rapid Prototyping 3D Printing
- Faster time to market
- Reduced development costs
- Sustainability
- Design flexibility
- Lower risk
- Minimizing waste
3D Printing Malaysia , 3D Printing Service Malaysia , 3D Printing service Singapore, Metal 3D Printing Malaysia
3D Printing service malaysia
Revolutionize Your Design Process with Rapid Prototyping
Your first product prototypes, but faster. Rapid prototyping is the practice of quickly fabricating physical parts, models or assemblies.
An initial prototype, created early in product development, allows for testing of appearance, functionality, and user experience.
It can range from a basic 3D-printed model reflecting the final product’s design to a more intricate version that tests performance, helping to identify and reduce potential risks. Prototyping ensures a stronger foundation for refined development.
A Guide to Selecting Manufacturing Processes for Initial Prototypes
The most cost-efficient technologies for manufacturing your initial prototypes are prototyping FDM and prototyping SLA (both 3D printing processes).
FDM is ideal for basic product models but lacks smooth surface finishes and complex part capabilities. In contrast, SLA provides enhanced geometric flexibility and is comparably priced for small Prototyping with SLA offers greater geometric flexibility compared to FDM, making it an excellent choice for creating complex designs at a comparable price for small batches.
Additionally, SLA excels in producing organic shapes, which often scale effectively for injection molding. This capability enhances the versatility and cost-effectiveness of your prototyping process.
3D Printing service Singapore , 3D Printing service Thailand , 3D Scanning Malaysia
Comparison of 3D Printing Processes
TECHNOLOGY | FDM | SLA | SLS | SLM | PµSL | MJF |
Build size | W500 x L500 x H500 mm | W600 × L350 × H350 mm | W350 X L350 X H590mm | W150 X L150 X H150mm | W100 X L100 X H50mm | W350 X L350 X H590mm |
Best lead time | 2day | 2day | 4day | 5day | 5day | 6day |
Dimensional accuracy | ± 0.3mm or lower | ± 0.3mm or lower | ± 0.3mm or lower | ± 0.3mm or lower | ± 0.2mm or lower | ± 0.3mm or lower |
Prototyping applications | Proof-of-concept prototypes from a wide range of materials. | Highly detailed visual prototypes. | Functional prototypes for testing and usability evaluations. | Metal prototypes with complex geometries. | Functional parts with small features and significant complexity. | High-fidelity functional parts for rigorous testing. |
End-use applications | Non-visual end parts, including precision jigs and fixtures. | Small aesthetic, non-functional end parts. | Low-volume functional end-use components. | Low-volume fully functional complex metal components. | Low-volume functional parts. | Low-volume functional end-use components. |
How do you move from initial prototyping to functional prototyping?
At the initial prototyping stage, the focus is on quickly assembling parts to address basic design challenges, not on presenting to investors. The goal is to test if the product features work as intended. Precision isn’t essential here, so parts can be sourced quickly and cost-effectively, allowing rapid adjustments.
In functional prototyping, however, component quality and materials become more critical. This stage evaluates whether the design effectively solves the intended problem, providing insights into future ROI. Parts should closely resemble the final product, and higher-end processes like SLS, MJF, or CNC machining are suitable—especially if metal components are involved.
For 3D printing, consider using a reliable bureau like Projet for quality results.
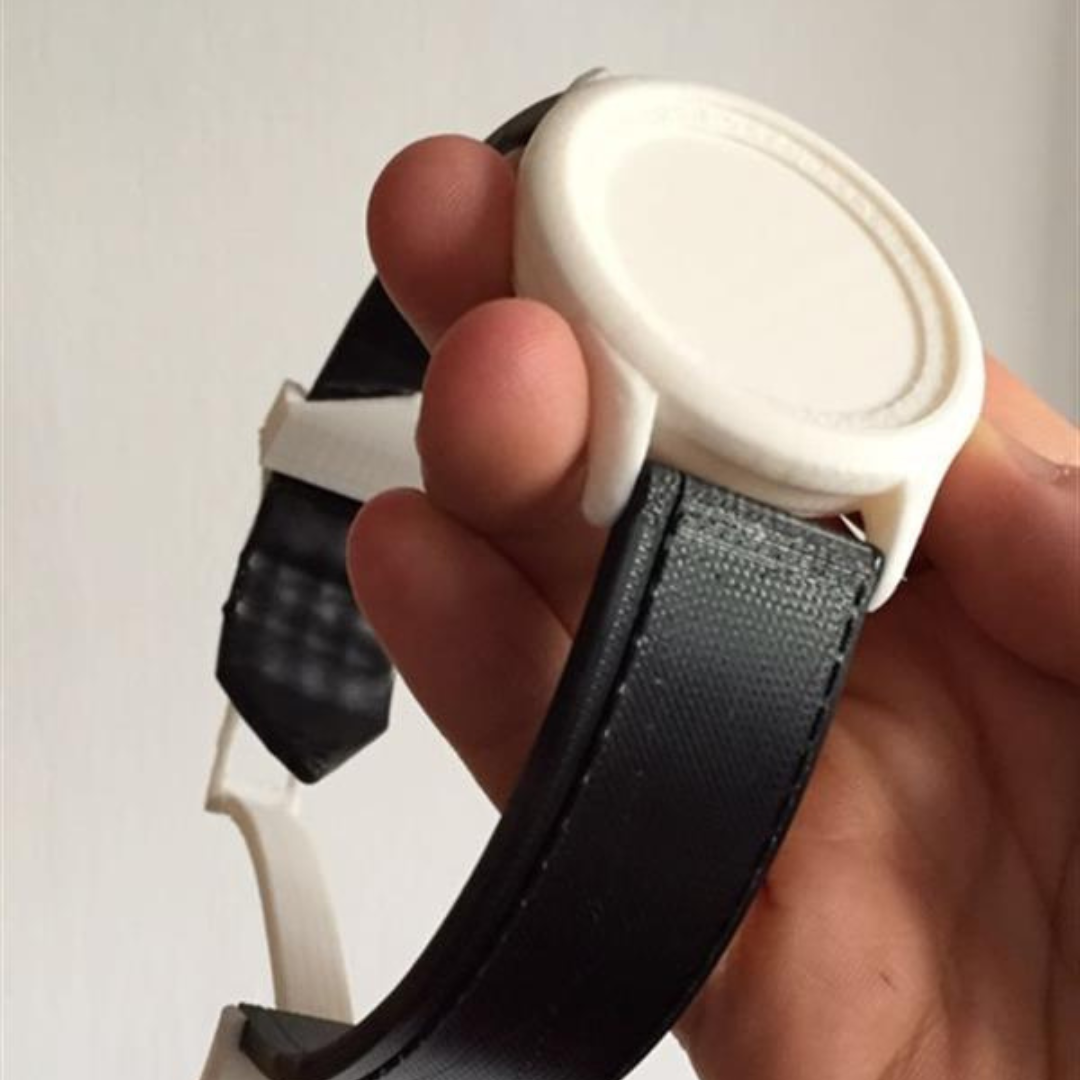
Print time and material
Print time in 3D printing depends on the number of material paths the printer must create for each layer. Infill prints quickly, while shells and supports print more slowly due to their larger surface areas. Factors like surface area, supports, and volume influence overall print time. Since volume is often difficult to adjust, reducing surface area and supports can effectively shorten print time. Similarly, material estimates are easy to calculate—minimizing supports reduces both print time and material usage, making the process more efficient.