FDM is an additive manufacturing process also known as 3D printing.
3D printing has emerged as a popular and efficient method for producing parts for both businesses and home users. Among the various technologies, Fused Deposition Modeling (FDM) stands out. This technique extrudes thermoplastic filament through a nozzle onto a build plate, offering speed and reliability. However, FDM does have limitations when working with advanced materials such as glass or ceramics.
Despite these constraints, FDM remains the most common 3D printing method. This article explores FDM’s definition, history, advantages, limitations, and compares it to other 3D printing techniques.
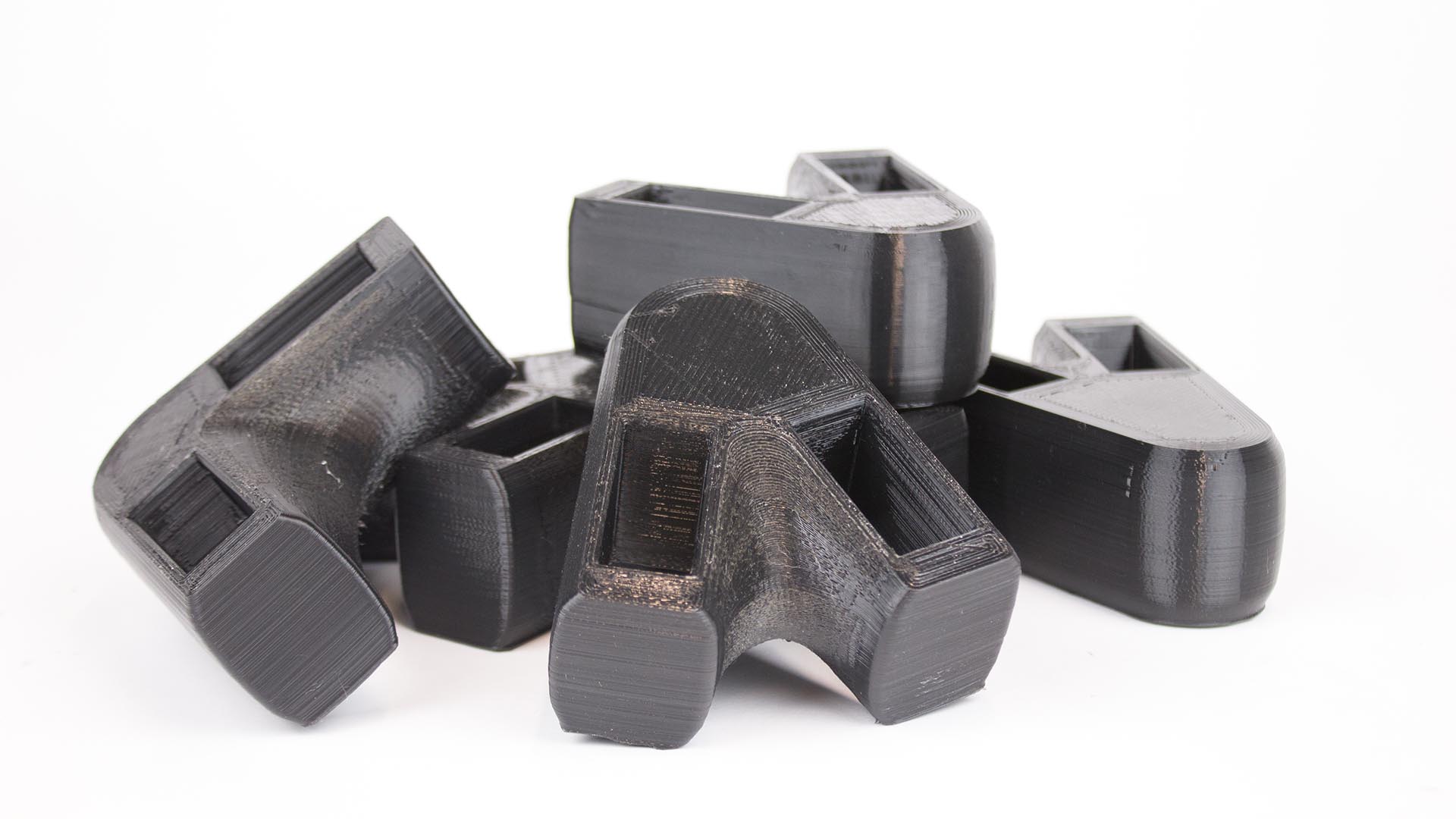
What is Fused Deposition Modeling (FDM) in 3D Printing?
Fused Deposition Modeling (FDM), also called Fused Filament Fabrication (FFF), is a popular additive manufacturing process classified under material extrusion. It builds objects by melting thermoplastic filament and precisely depositing it layer-by-layer along a pre-set path.
Its precision and material efficiency make it a go-to choice for prototyping and production in various industries.
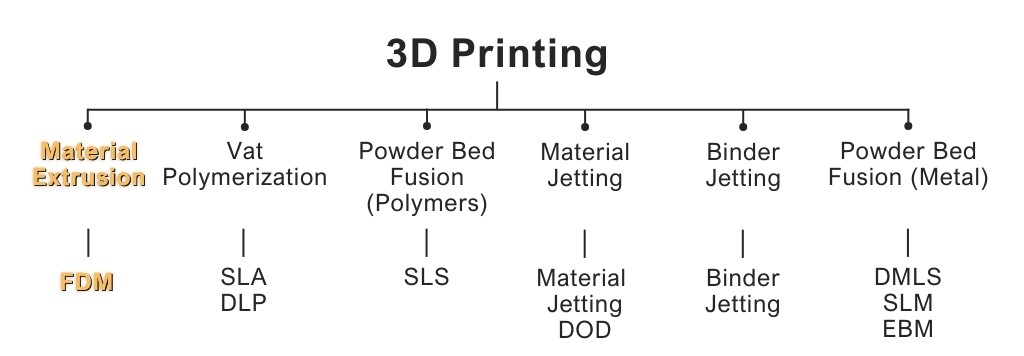
How FDM Printing Works ?
FDM printing uses CAD files, mainly in STL format, to create 3D objects by layering thermoplastic filament. The process starts by uncoiling the filament, which is heated and precisely extruded onto a platform. A computer controls the nozzle’s movements across X, Y, and Z dimensions.
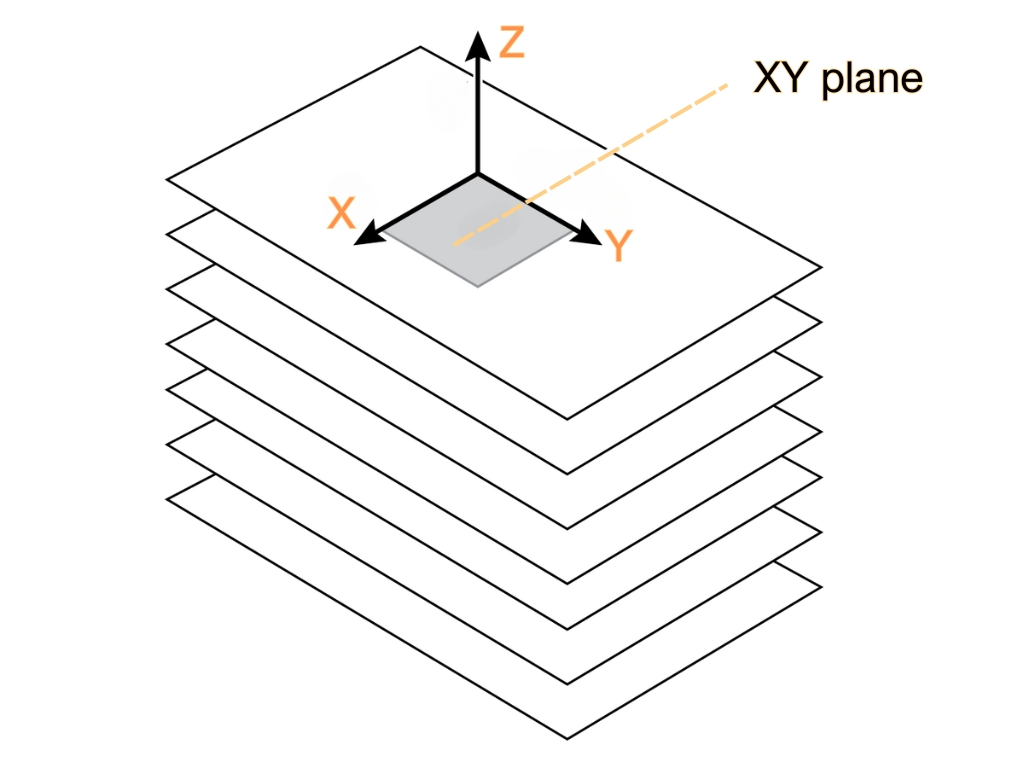
3D-printed parts tend to be stronger along the XY plane, which runs parallel to the print bed, compared to the Z axis, which is perpendicular to the print bed.
3D Printing service malaysia
An FDM 3D printer operates by depositing melted filament material layer by layer onto a build platform, ultimately creating a completed part. It utilizes digital design files uploaded to the machine, which translate these designs into precise physical dimensions. The materials used for FDM printing include various polymers such as ABS, PLA, PETG, PA, and TPU, which the machine feeds through a heated nozzle.
To start operating an FDM printer, first, load a spool of thermoplastic filament into the device. Once the nozzle reaches the optimal temperature, the printer feeds the filament through the extrusion head and nozzle. The extrusion head is mounted on a three-axis system, allowing movement along the X, Y, and Z axes. The printer then extrudes melted material in thin strands, depositing it layer by layer based on the design specifications.
This streamlined process ensures high-quality prints and efficient operation of FDM printer.
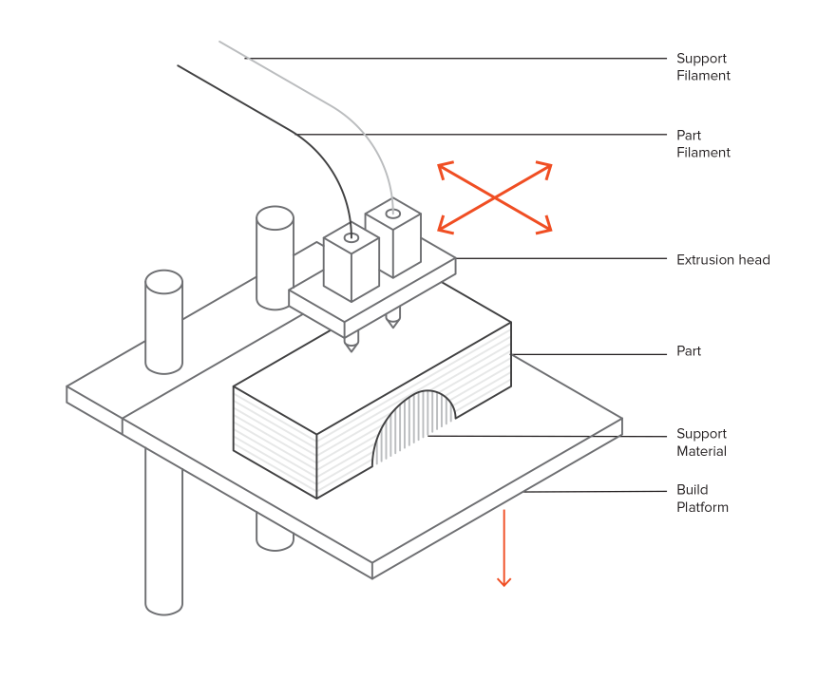
Filling an area requires multiple passes, akin to coloring within the lines with a marker. After completing one layer, the build platform descends, allowing the machine to begin the next layer. In certain setups, the extrusion head may also move upward. The process continues until the part is completely finished.
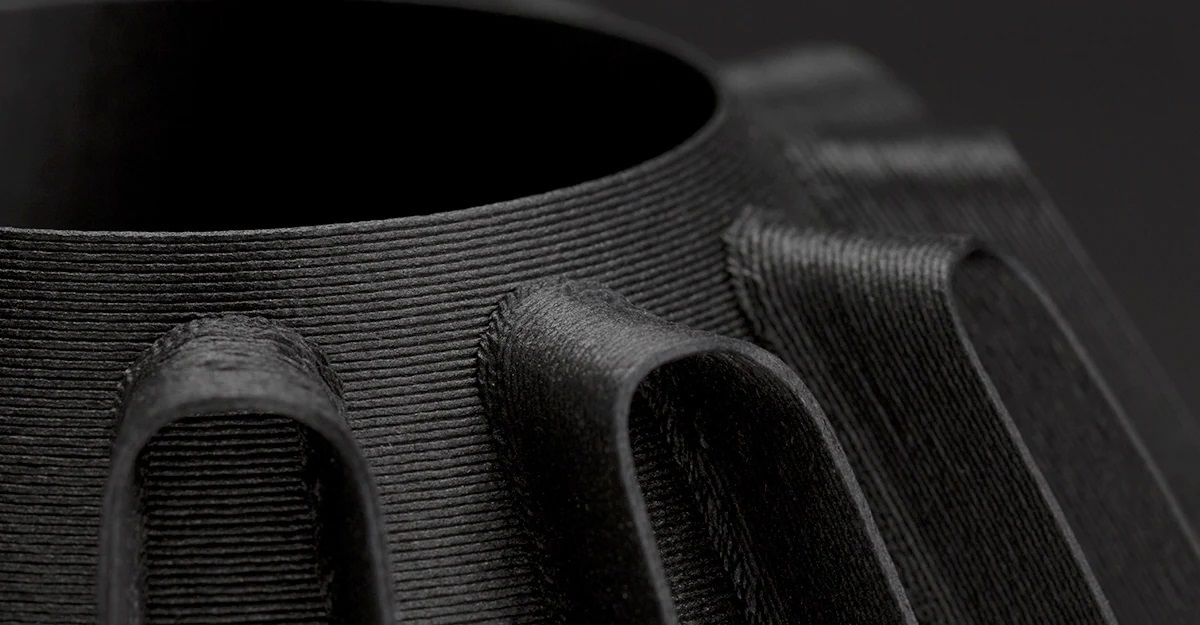
Closeup of FDM part showing layers.
Infill and shell thickness
To minimize print time and conserve materials, FDM printers typically avoid creating solid parts. Instead, these machines outline the outer perimeter, known as the shell, through multiple passes and fill the interior, referred to as the infill, with a low-density internal structure. The thickness of both the infill and shell plays a crucial role in the strength of FDM-printed components. Most desktop FDM printers default to a 20% infill density and a 1 mm shell thickness, striking a balance between strength and speed for efficient printing.
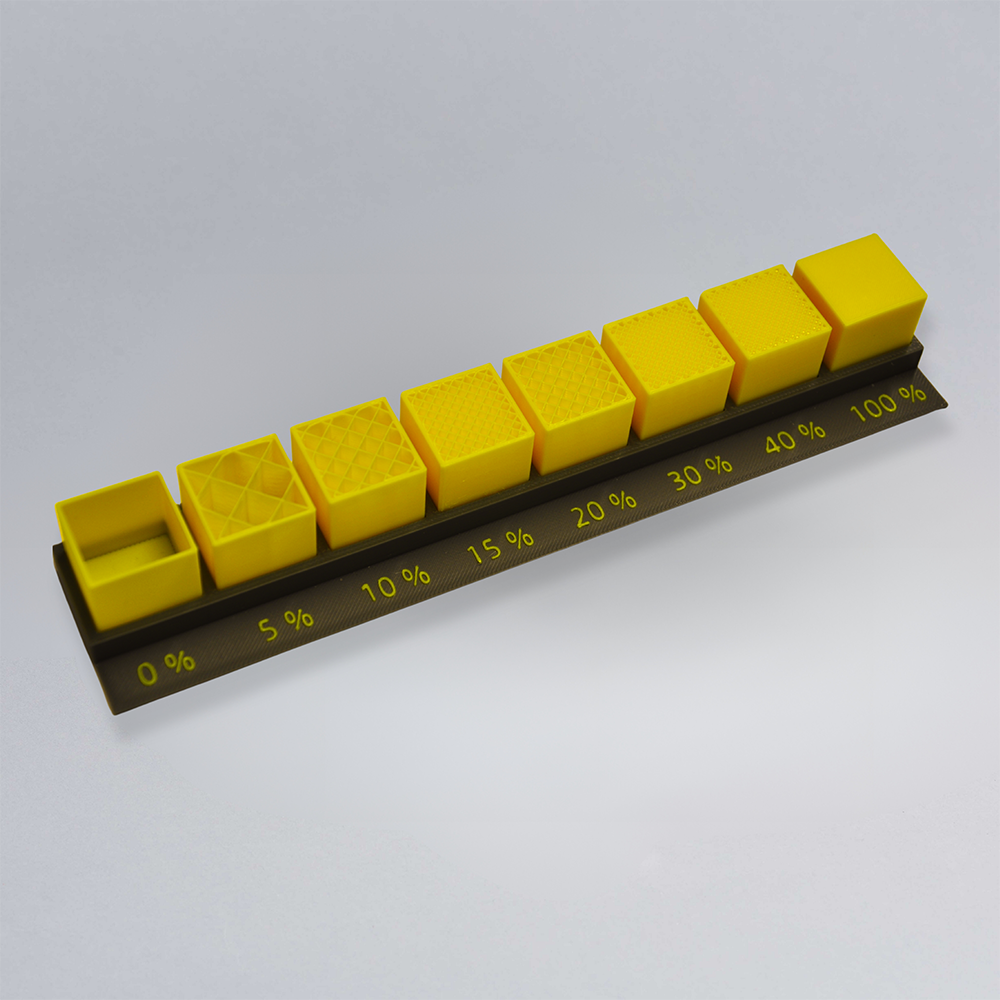
Print time and material
Print time in 3D printing depends on the number of material paths the printer must create for each layer. Infill prints quickly, while shells and supports print more slowly due to their larger surface areas. Factors like surface area, supports, and volume influence overall print time. Since volume is often difficult to adjust, reducing surface area and supports can effectively shorten print time. Similarly, material estimates are easy to calculate—minimizing supports reduces both print time and material usage, making the process more efficient.
Common Materials Used in FDM 3D Printing
- Acrylonitrile Butadiene Styrene (ABS) is a thermoplastic polymer renowned for its rigidity, weldability, and high impact resistance. It excels in applications requiring toughness and heat resistance, commonly found in kitchenware, surgical instruments, and toys like LEGO blocks.
- Polylactic Acid (PLA) is a biodegradable polymer derived from renewable resources such as cornstarch and sugar cane. Its brittleness makes it suitable for the food and health industries, particularly in surgical applications.
- Polyethylene Terephthalate Glycol (PETG) is a modified PET known for its strength and ease of printing. Its chemical resistance and transparency make it ideal for containers, graphic displays, and textiles.
- Thermoplastic Polyurethane (TPU) boasts excellent mechanical properties and rubber-like elasticity, making it widely used in automotive, footwear, and sports equipment applications that require flexibility.
- Nylon (PA) is prized for its exceptional strength and resistance to wear and chemicals. It’s perfect for non-flexible filaments and applications demanding durable materials.
Limitations of FDM Technology
Fused Deposition Modeling (FDM) technology presents several limitations that impact its effectiveness in industrial applications. These constraints primarily revolve around the materials it can utilize, the precision of intricate designs, and the overall print quality. Below are the key limitations:
Material Availability: One significant limitation of FDM technology is its restricted material options. Unlike other 3D printing methods, FDM cannot use advanced materials such as glass and ceramics. Although it can print with engineering-grade thermoplastics, these materials often fall short in terms of strength and durability compared to alternatives offered by other 3D printing technologies.
Quality Issues of Finished Products: Parts created through FDM are often anisotropic, meaning they are more susceptible to breaking under compressive forces applied parallel to the layer lines. Moreover, visible lines between the printed layers can compromise the aesthetic quality of the final product. Although chemical and mechanical polishing can mitigate this issue, these processes require additional labor and time.
Challenges in Printing Highly Detailed Objects: FDM typically produces parts with a resolution of about 100 microns, which is insufficient for intricate designs. The standard nozzle size of 0.4 mm further restricts the creation of small, detailed components. While it is possible to switch to a 0.2 mm nozzle, the precision still does not match that of other technologies like Selective Laser Sintering (SLS) or Stereolithography (SLA).
History of Fused Deposition Modeling (FDM)
Fused Deposition Modeling (FDM) has been pivotal in 3D printing’s development. Invented by S. Scott Crump in the late 1980s and commercialized through Stratasys in 1990, FDM technology remains central to the industry. In 2005, the open-source RepRap movement significantly advanced FDM by encouraging users to 3D print their own printer parts and assemble them.
Summary
Projet offer a range of capabilities, including laser cutting, laser engraving and others, along with various solutions like rapid prototyping, mechanical design, and reverse engineering. We eagerly anticipate the opportunity to support your company in its processes.
Connect with Projet:
If you’ve had a positive experience with Projet that you’d like to share, please reach out to us at [email protected]. We eagerly anticipate hearing from you.
For additional information, visit our website for comprehensive details about our services and contact information. Our friendly team is ready to assist you at any time.