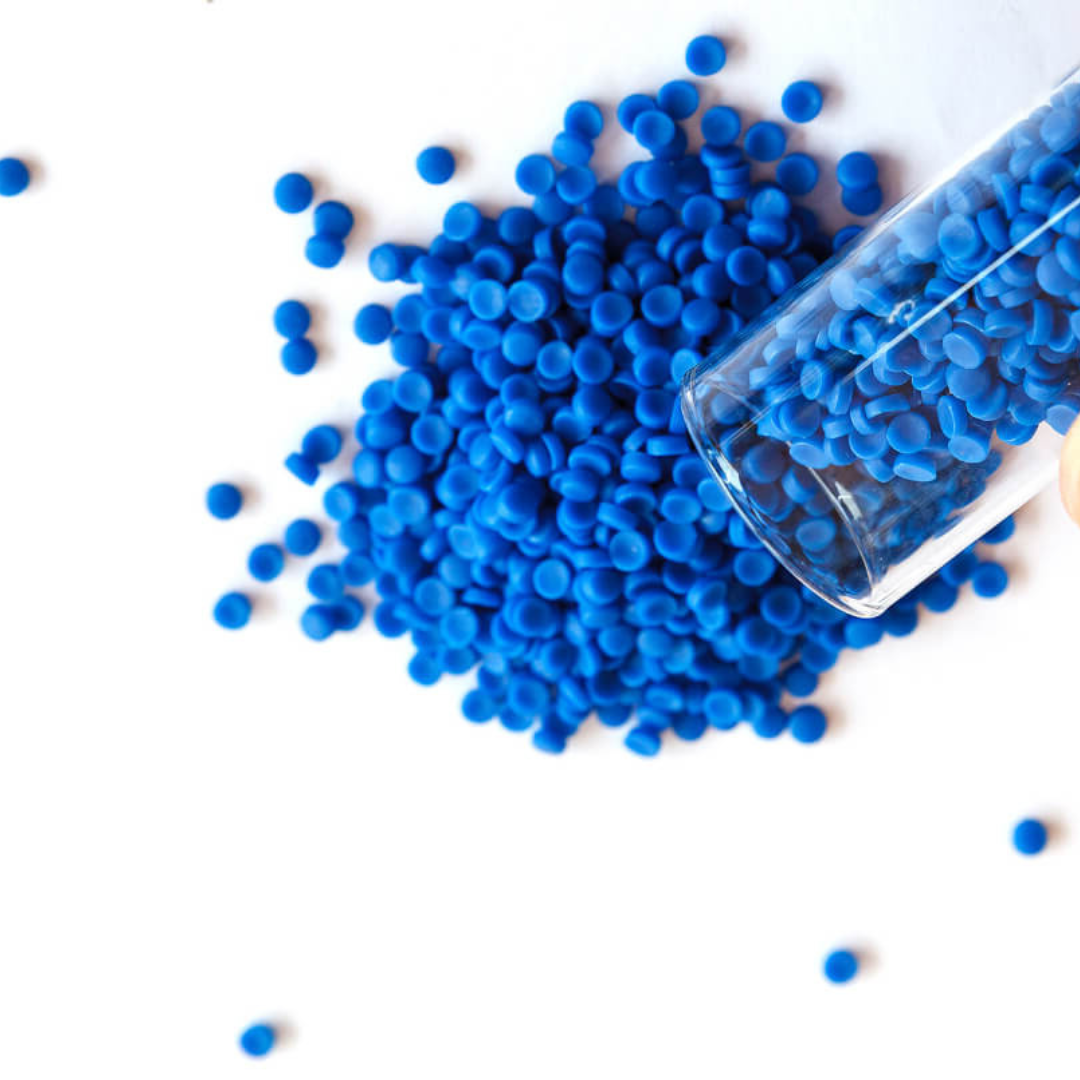
PETG(Polyethylene Terephthalate Glycol), and PP(Polypropylene) are among the most commonly used plastics, and understanding their key differences is essential for choosing the right material for specific applications. This article provides a comprehensive comparison between PETG and PP, guiding you to make informed decisions for your projects. Whether you’re evaluating strength, flexibility, or cost, this resource will help you select the most suitable plastic for your needs.
What is Polypropylene (PP) ?
Polypropylene (PP) is highly valued for its high melting point, flexibility, and strong chemical resistance, making it ideal for applications in packaging, automotive, and textiles.. Its heat-resistant properties are perfect for creating durable containers, bottles, and packaging films. Additionally, PP’s excellent fatigue resistance increases its versatility in industrial applications. These attributes make PP a preferred material across industries, especially in areas requiring durability and high heat tolerance.
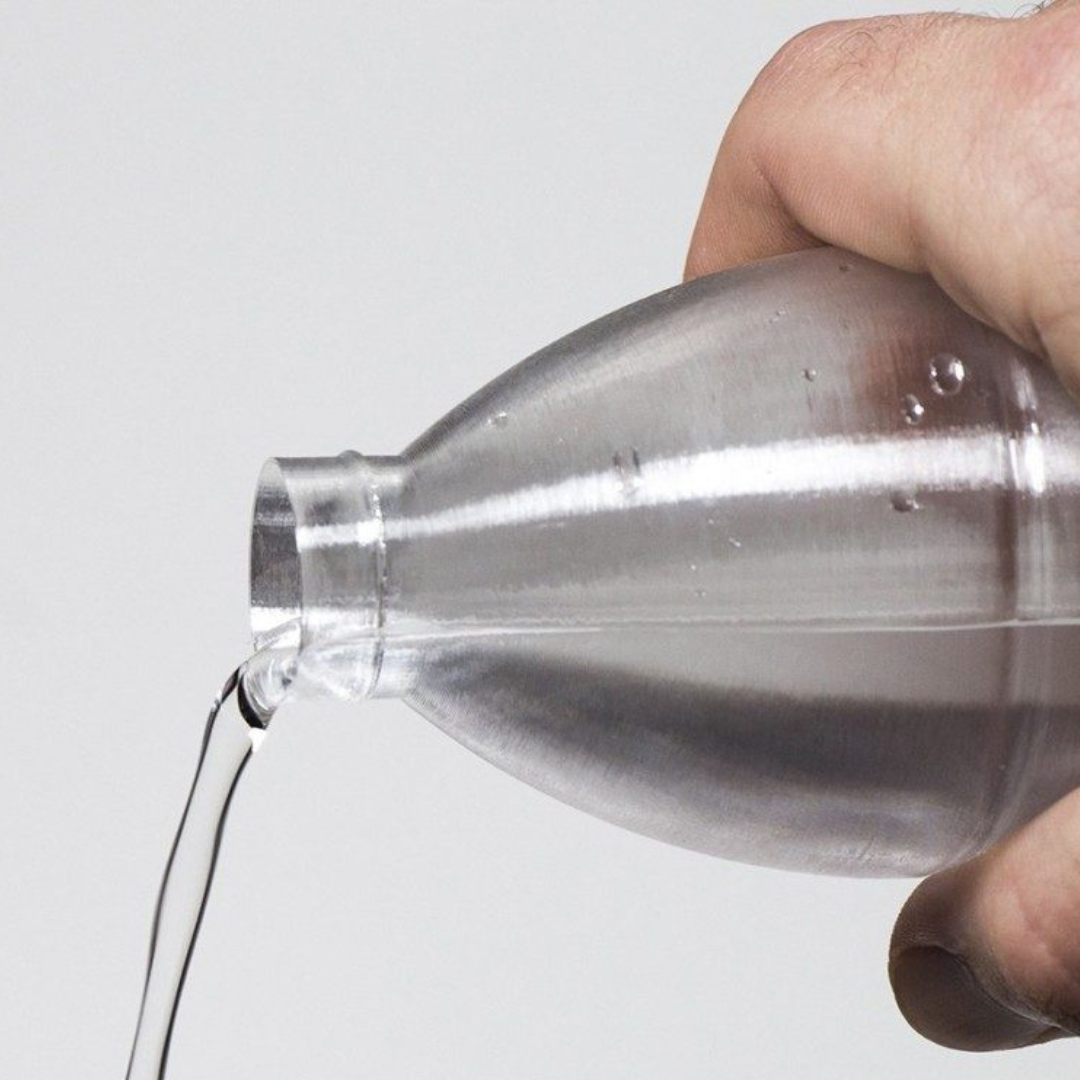
What is Polyethylene Terephthalate Glycol (PETG) ?
The “G” in PETG stands for “Glycol,” which improves PET by enhancing its chemical resistance and formability. Glycol addresses common PET issues like cloudiness and fragility, making PETG a more durable and versatile thermoplastic polyester. PETG is known for being non-toxic, odorless, and chemically resistant, making it an ideal choice for food containers, beverage bottles, and various manufacturing processes.
The comparison of PET vs. PP in chemical resistance?
PETG (Polyethylene Terephthalate Glycol)
PETG offers strong resistance to water-based chemicals, including common substances like alcohol and weak acids. However, it is less resistant to stronger acids, bases, and some solvents. Due to its combination of clarity and toughness, PETG is widely used in various applications, particularly in medical devices, food packaging, and 3D printing. This makes it a versatile material for industries that require both durability and transparency.
PP (Polypropylene)
Polypropylene (PP) is valued for its excellent chemical and moisture resistance, making it ideal for applications like automotive parts, laboratory equipment, and food containers that require durability and heat tolerance.
The comparison of PET vs. PP in temperature tolerance?
PETG (Polyethylene Terephthalate Glycol)
PETG offers excellent thermal stability, tolerating temperatures up to 85°C (185°F), making it suitable for applications needing moderate heat resistance. It is widely used in industries like 3D printing, medical devices, and food packaging due to its clarity, toughness, and safety. PETG’s combination of durability and visual quality ensures consistent performance in sectors where these properties are critical, making it a versatile material for both functional and aesthetic purposes.
PP (Polypropylene)
Polypropylene (PP) is a durable material with excellent thermal resistance, tolerating temperatures up to 100°C. It is widely used in automotive spare parts, lab equipment, and dishwasher-safe food containers.
The comparison of PET vs. PP in mechanical strength?
PETG (Polyethylene Terephthalate Glycol)
- Tensile Strength: PETG has a high tensile strength, typically around 53 MPa. This makes it strong and resistant to stretching and breaking.
- Impact Resistance: PETG offers good impact resistance, which means it can absorb significant energy without fracturing.
- Flexural Strength: PETG has a flexural strength of about 77 MPa, providing good resistance to bending forces.
PP (Polypropylene)
- Tensile Strength: PP has a tensile strength that can range from 36 to 93 MPa, depending on the specific type and formulation.
- Impact Resistance: PP also has good impact resistance, but it may not perform as well as PETG at lower temperatures.
- Flex Fatigue Resistance: PP is highly resistant to flex fatigue, making it ideal for applications like living hinges that require repeated bending.
The comparison of PET vs. PP in barrier properties?
PETG (Polyethylene Terephthalate Glycol)
- Moisture Barrier: PETG provides a moderate moisture barrier, which is suitable for many packaging applications.
Oxygen Barrier: PETG has a good oxygen barrier, making it effective for packaging that requires protection from oxidation.
Chemical Barrier: PETG offers good resistance to water-based chemicals and common substances like alcohol and weak acids.
PP (Polypropylene)
- Moisture Barrier: Polypropylene (PP) offers outstanding moisture barrier properties, effectively preventing moisture ingress and providing reliable protection.
Oxygen Barrier: PP generally has a lower oxygen barrier compared to PETG, which can be a limitation for certain applications.
Chemical Barrier: PP provides excellent resistance to a wide range of chemicals, including acids, bases, and organic solvents.
Summary
Projet offer a range of capabilities, including laser cutting, laser engraving and others, along with various solutions like rapid prototyping, mechanical design, and reverse engineering. We eagerly anticipate the opportunity to support your company in its processes.
Connect with Projet:
If you’ve had a positive experience with Projet that you’d like to share, please reach out to us at [email protected]. We eagerly anticipate hearing from you.
For additional information, visit our website for comprehensive details about our services and contact information. Our friendly team is ready to assist you at any time.