The aerospace industry has long been a trailblazer in the adoption of 3D printing, also known as additive manufacturing. Since the 1980s, OEMs, suppliers, and government agencies have been leveraging this innovative technology. Today, modern commercial airplanes incorporate over 1,000 3D-printed parts, highlighting the transformative impact of 3D printing on the industry.
Since its early adoption in 1989, the aerospace sector has played a pivotal role in advancing 3D printing technology and processes, establishing itself as one of the key contributors to the evolution of this field.
Applications of 3D Printing in Aerospace
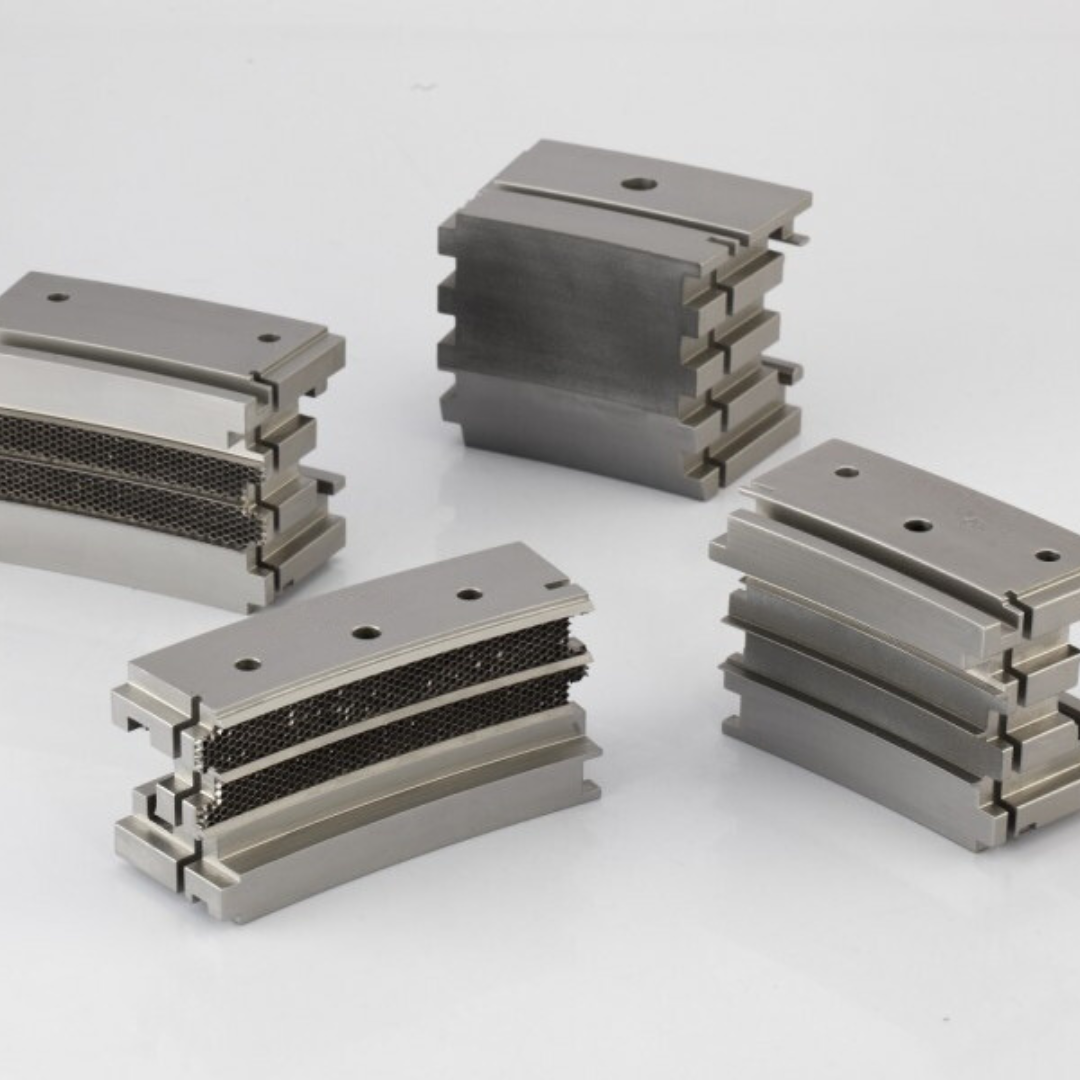
Engine Components:
The materials used for engine components must withstand high mechanical and thermal stresses. Parts like turbine shrouds can be made by 3D printing processes like SLM (Selective Laser Melting). Not only is the production of shrouds using these processes more efficient, but the shrouds themselves are lighter than those made by traditional manufacturing methods.
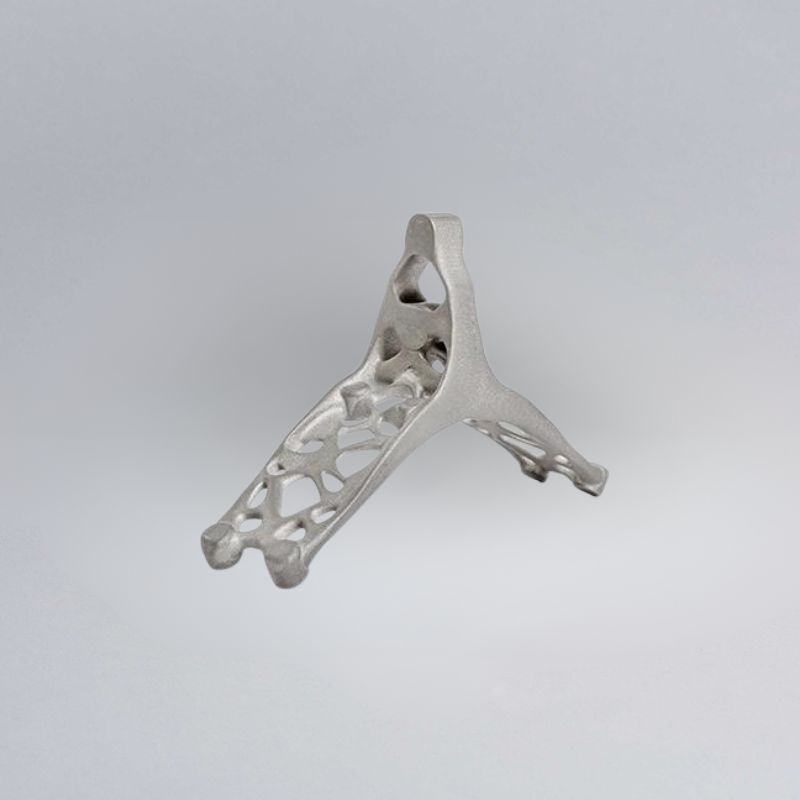
Structural Components:
Structural components, both interior and exterior, form and support an aircraft’s rigid body. Through 3D printing methods like SLM and FFF, components such as brackets and inserts can be crafted using materials like titanium, copper, and nickel alloys.
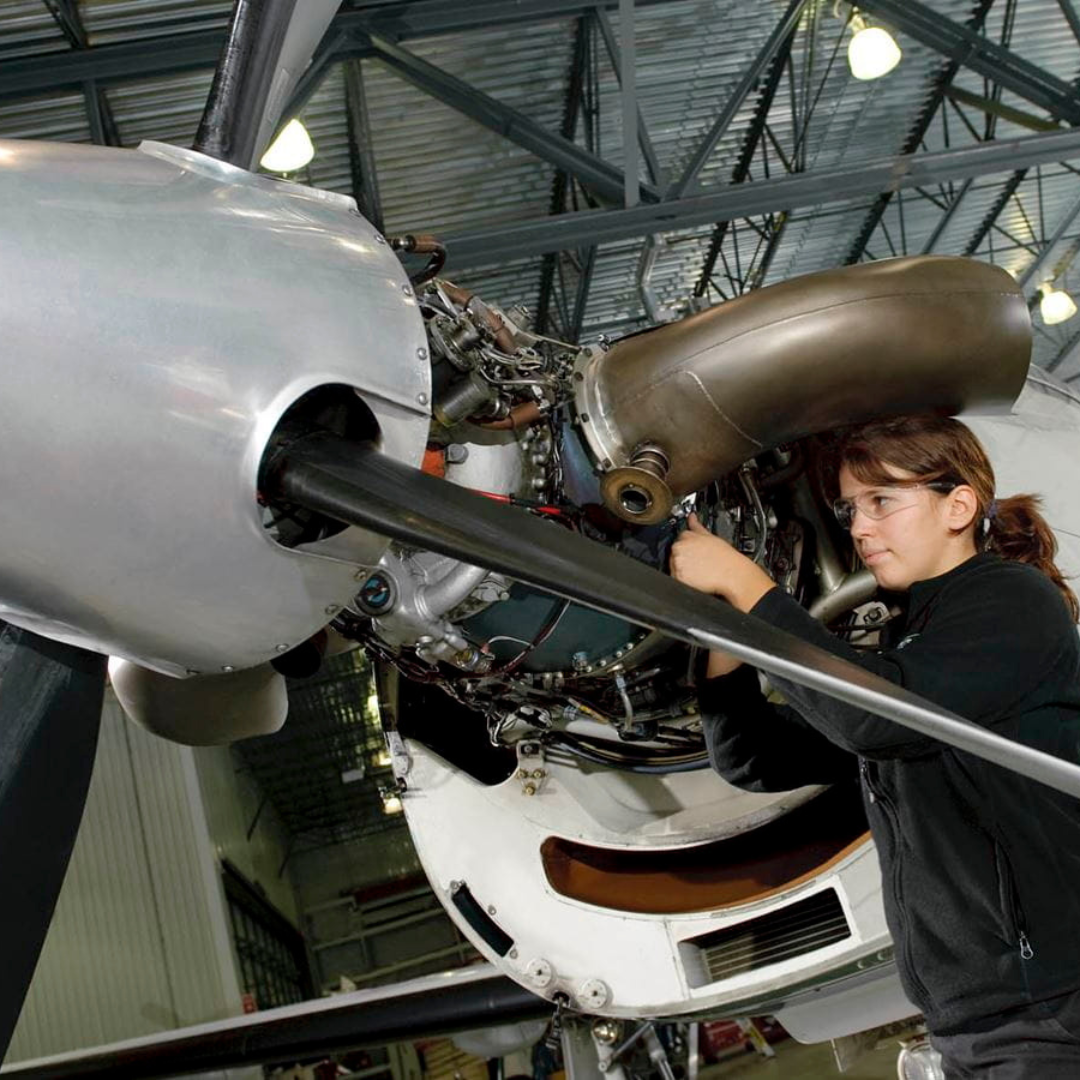
Maintenance & Repair:
Regular maintenance and repair are essential for aircraft safety and longevity. Advanced 3D printing techniques, such as SLM and FFF, enable the efficient fabrication of jigs, fixtures, and tools from titanium, stainless steel, and other metals, streamlining aircraft maintenance processes. Embracing these technologies enhances reliability and extends aircraft lifespan.
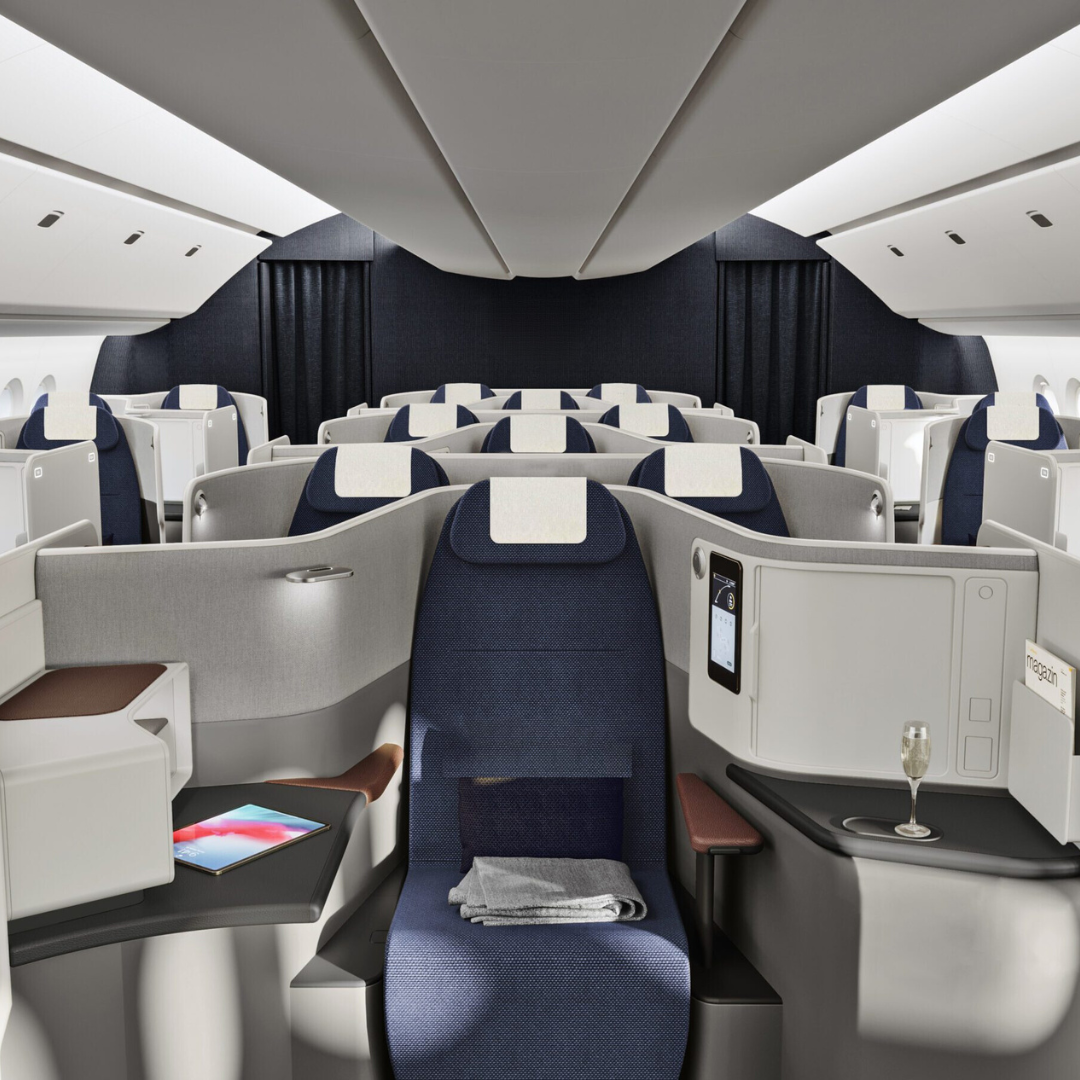
Interior Components:
Aircraft interior components range from avionics equipment to cabin accessories like galley inserts and light fixtures. Popular 3D printing methods such as SLA (stereolithography) and SLS (selective laser sintering) are widely used to fabricate these essential parts, offering precision and efficiency in aerospace manufacturing..
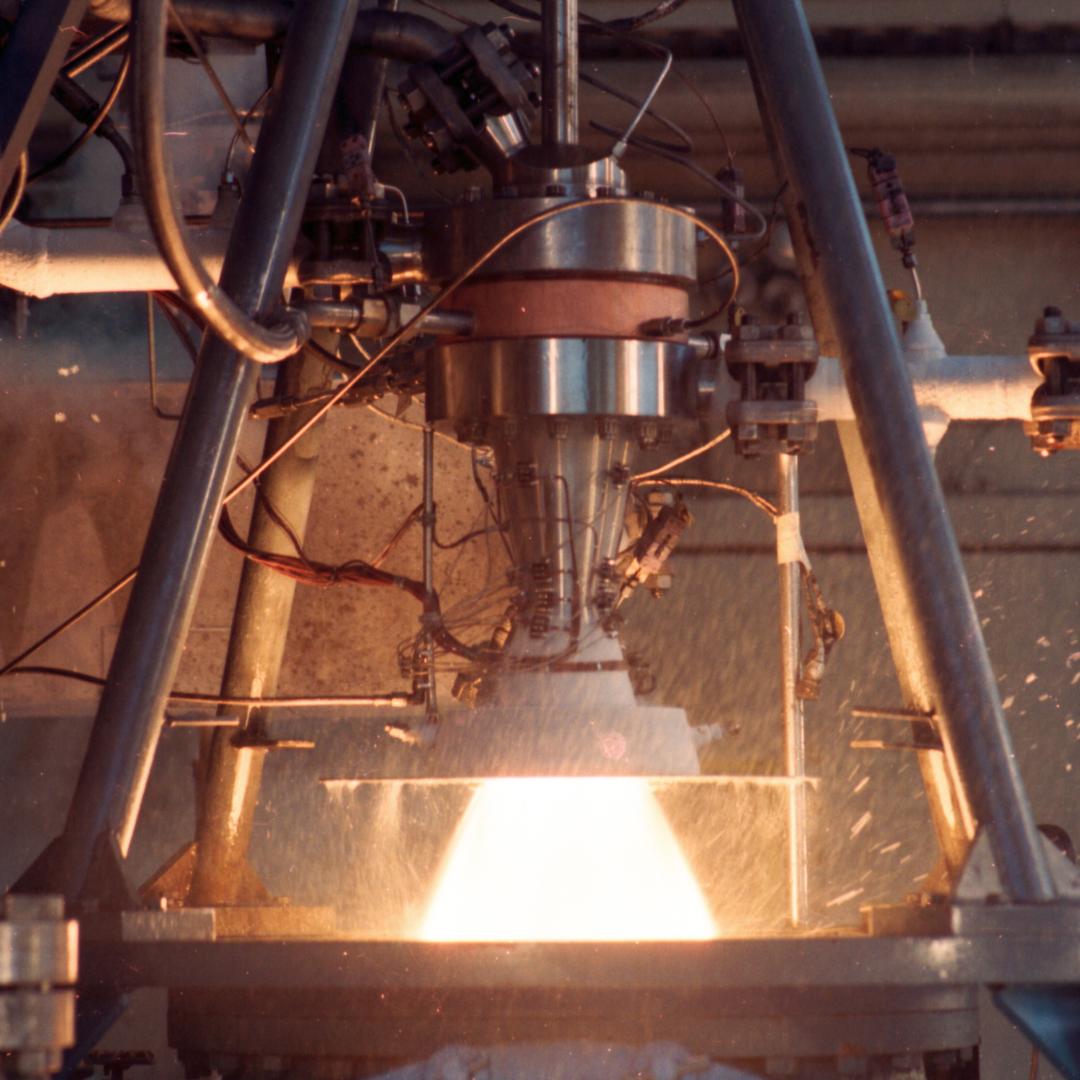
Prototyping & Toolings:
Prototyping and tooling are essential for designing and testing new concepts, especially in aerospace. 3D printing excels in this domain, enabling rapid creation of complex parts like suspension wishbones , masking jigs with minimal setup. This on-demand capability accelerates product development and testing, enhancing innovation and efficiency.
3D Printed Aerospace Parts:
- electrical components
- microchip components
- microfluidic devices
- drug-delivery microneedles
- vascular stents
- micro-scale molds
- electro-mechanical parts for optics & photonics
Among the various 3D printing technologies:
- Stereolithography (SLA):
SLA technology enables the production of high-precision prototypes and parts with exceptionally smooth surfaces. Its ability to create intricate details makes it an ideal choice for manufacturing complex components, such as sensor housings and aerodynamic part prototypes. - Selective Laser Sintering (SLS):
This technology leverages laser-based techniques to melt and solidify thermoplastic powders, making it highly effective for producing components from polyamide and other thermoplastic materials. This approach offers significant advantages, particularly in the manufacturing of complex, high-quality parts. - Selective Laser Metal (SLM):
SLM is a crucial technology for producing complex, high-performance metal parts. By selectively melting successive layers of powder through the precise interaction of a laser beam, SLM enables the creation of strong, lightweight components that are ideal for aerospace applications. This advanced technique is essential for manufacturing engine components, structural support systems, and other critical parts that ensure aircraft safety and optimal performance. - Fused Filament Fabrication (FFF):
FFF often referred to as filament 3D printing, is a popular technique that utilizes a filament of fused plastic material to build objects layer by layer. This method is extensively used for creating prototypes and components that are not subject to high stress. Although parts produced via FFF may generally be less durable compared to those made with other techniques, it provides notable advantages in terms of flexibility and production speed.
Connect with Projet:
If you’ve had a positive experience with Projet that you’d like to share, please reach out to us at [email protected]. We eagerly anticipate hearing from you.
For additional information, visit our website for comprehensive details about our services and contact information. Our friendly team is ready to assist you at any time.